25 - 08 - 2020
A thought-piece by BPTW – first published by RICS Built Environment Journal on 25 August.
At the Beechwood Village development in Basildon, England, architectural firm BPTW have carefully developed a range of standard house typologies for Swan NU Living, the development arm of Swan Housing Group. The development consists of 96 homes delivered as a series of sensitively inserted infill developments which will transform what was previously a local authority estate into a reimagined neighbourhood. All the houses here will be constructed using Swan’s cross laminated timber (CLT) modular system, manufactured locally by Swan’s own NU Build factory in Basildon.
It is generally understood that if the benefits of modular and off-site construction are to be maximised, the desired techniques must be identified and embedded into the design and decision-making process from the outset. Any additional time invested in design early on can be repaid later through increased build quality and speed as well as reductions in costs on site.
However, it is also important to understand that optimising the product development stage presents even greater long-term benefits, through the adoption of standardised typologies capable of being reused over multiple projects. This avoids the repetition of product design development and enhances the potential for economies of scale across multiple projects, maintaining a steady flow of high-quality homes, driving quality up and costs down as well as streamlining the procurement process.
Beechwood Village challenges a common misconception that modular construction is a barrier to good housing design and characterful places. It will see the complete redevelopment and regeneration of the Craylands Estate, where poor planning created fundamental failures in the existing layout, and left a legacy of many homes no longer fit for purpose or unsuited to improvement. The lack of traditional street patterns in the existing estate resulted in a poor-quality public realm which will be transformed through the selective demolition of existing homes and sensitive insertion of new houses. This will repair the urban fabric to create traditional streets linking public spaces and local amenities.
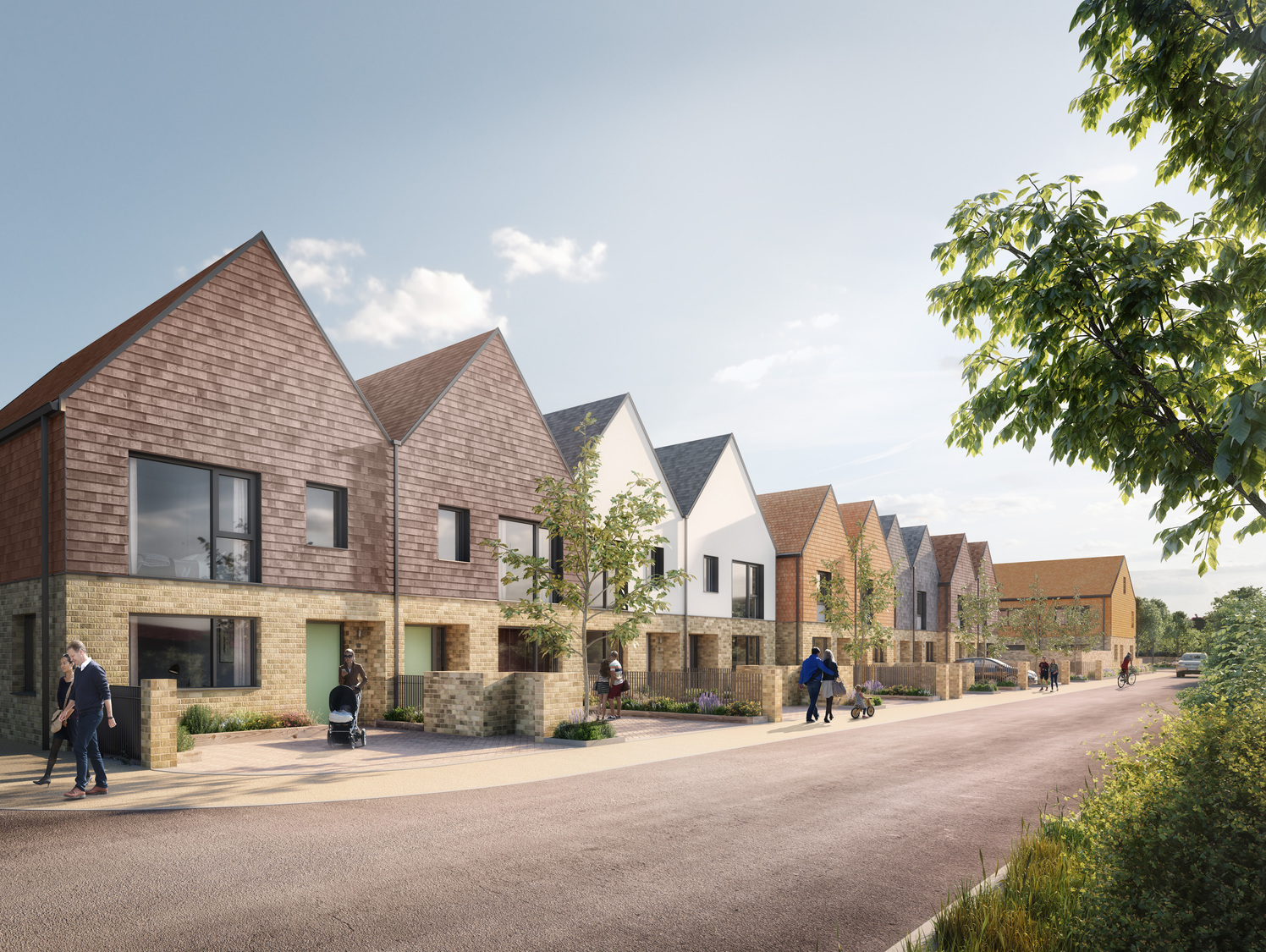
The design approach was informed from the outset by the nature of the CLT modular system and developed to exploit its strengths. A balance was struck between the benefits of repetition and the need for appropriate levels of variety required to support a distinctive placemaking strategy by using only four house types. These include wide and narrow frontage typologies, incorporating mews with under croft parking or on-street solutions, seamlessly integrating parking while maintaining a high quality of public realm. By mixing and matching different house types, gable or eaves fronted roofs and material finish, the opportunity to create variety and visual interest addressing household sizes and tenures as well as market demands is virtually limitless.
The extensive use of off-site manufacturing at Beechwood North also delivers other important benefits for the community and developer alike on a regeneration project such as this. The speed of the construction phase, and the associated reduction in site traffic, noise and pollution will minimise disruption to the residents and surrounding area, protecting the health and wellbeing of the local community.
At Beechwood, external materials are constructed on site, offering further flexibility to customise the development to reflect the local vernacular and create a distinctive place. External materials have been selected to complement both the original estate and the new homes, while the changes in material and colour reflect the tiled facades of the estate which have been painted different colours over time, creating a lively visual character.
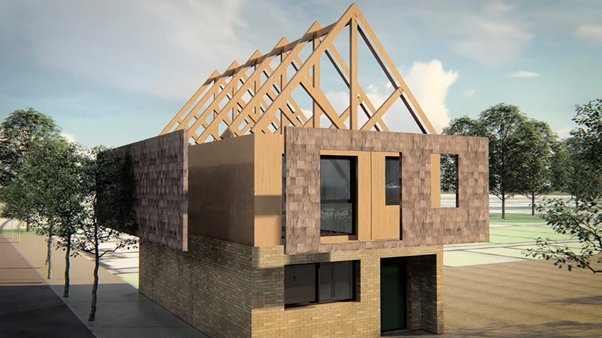
The efficiency of factory delivery was central to the design development at all stages of the creative process. This included the development of one house type that could be formed from a single width volumetric unit, with a second house type designed to use the same ground floor module as the first, further enhancing efficiency with a shared chassis. Each of the house types were designed to be orthogonal, without steps or staggers and with simple pitched roof forms to ensure ease of manufacture and optimising the efficiencies of the CLT system.
BPTW were appointed through all the RIBA plan of work stages, and discussions about the modular system were ongoing from feasibility stages in parallel with the planning design of the scheme. As designs developed through planning, the BPTW team and other consultants attended a regular series of project meetings to review the lessons learned from the factory process. Developing designs were reviewed by Swan’s modular design manager during workshops at the NU Build factory, and revisions were made to respond to the parameters of the CLT system.
Digital technology
Digital technology goes hand in hand with design, and this work was undertaken using Revit software, with BPTW leading a collaborative process in the BIM manager role. Having responsibility for the creation of the BIM protocols and the execution plan ensured that there was full coordination between disciplines to produce a data rich and consolidated three-dimensional model.
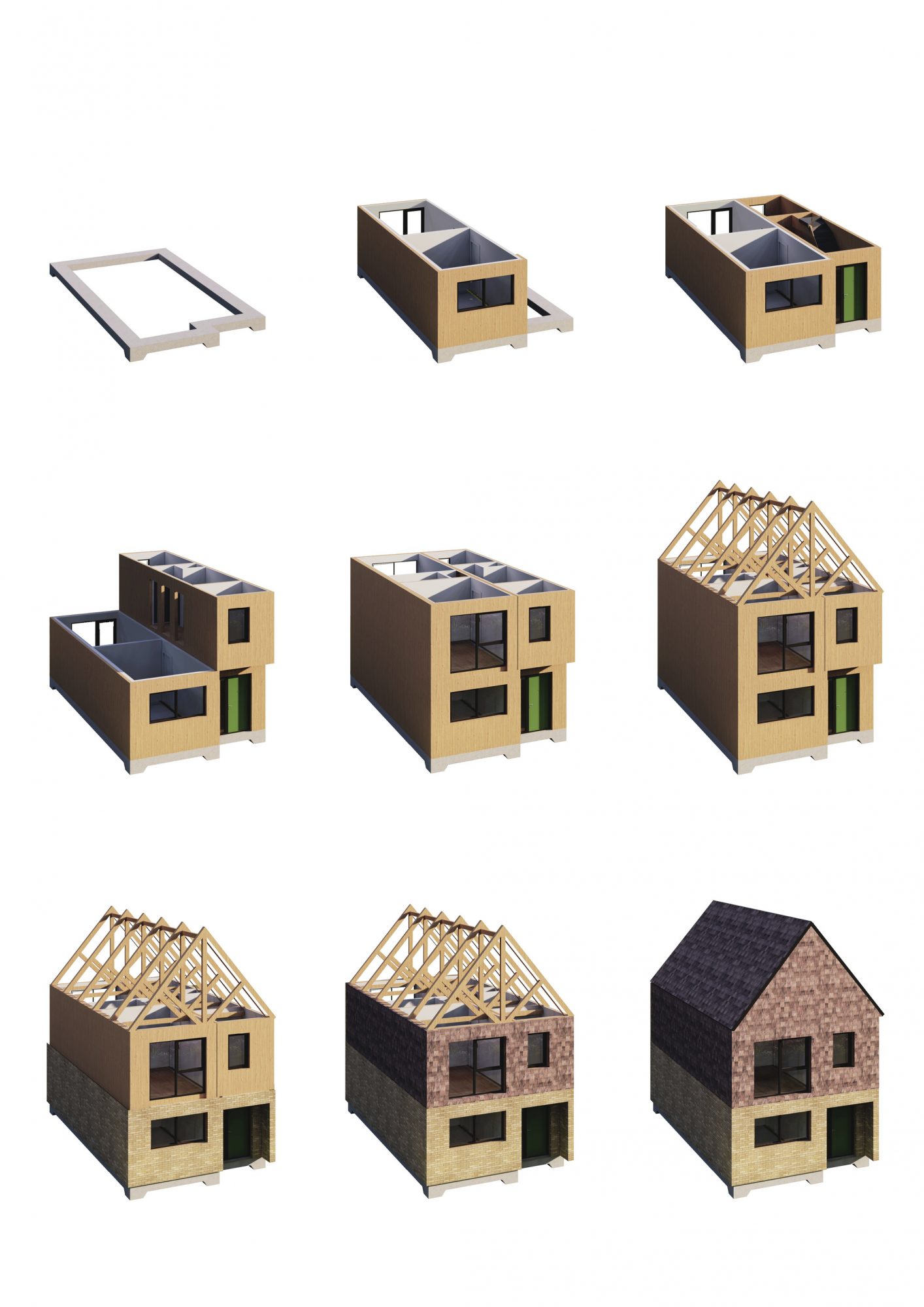
Clash detection workshops were regularly performed to highlight potential issues in order to resolve them in advance of manufacture. This produced a model fit not just for factory fabrication but also capable of further development to provide Swan’s housing management team with a facilities management tool covering the lifetime of the buildings.
Sustainability
The design for manufacture process offers enormous potential for enhanced levels of sustainability. Demands for increased fabric performance in order to contribute to net zero carbon targets will require the construction industry to deliver improved airtightness and minimal thermal bridges as standard.
Factory production can deliver more certainty regarding quality and precision as well as the ability to factory test prior to installation on site. Supply chain relationships can facilitate the sourcing and use of materials and components with reduced embodied carbon and increased use of recycled materials.
Off-site manufacture and modular construction techniques promote the creation of assemblies of components that can be easily installed, maintained or replaced as required. A process of assembly and disassembly using mechanical fixings will offer significant reductions to lifecycle costs going forward.
The impact of transportation and carbon emissions associated with multiple inefficient deliveries to site can also be reduced. Most critically, by its nature CLT offers enormous carbon benefits over other materials such as concrete or steel as timber sequesters carbon, effectively capturing and storing away atmospheric carbon dioxide.
Factory fabrication could initiate a smart technology revolution in mainstream housing, making this a feature for all rather than a luxury item for the few. A fully integrated approach to services and their controls ranging from heating, ventilation, lighting and security offers the potential for a total home management system that will bring convenience but also the potential to optimise comfort levels, health and wellbeing benefits for occupants alongside energy efficiency and environmental benefits.
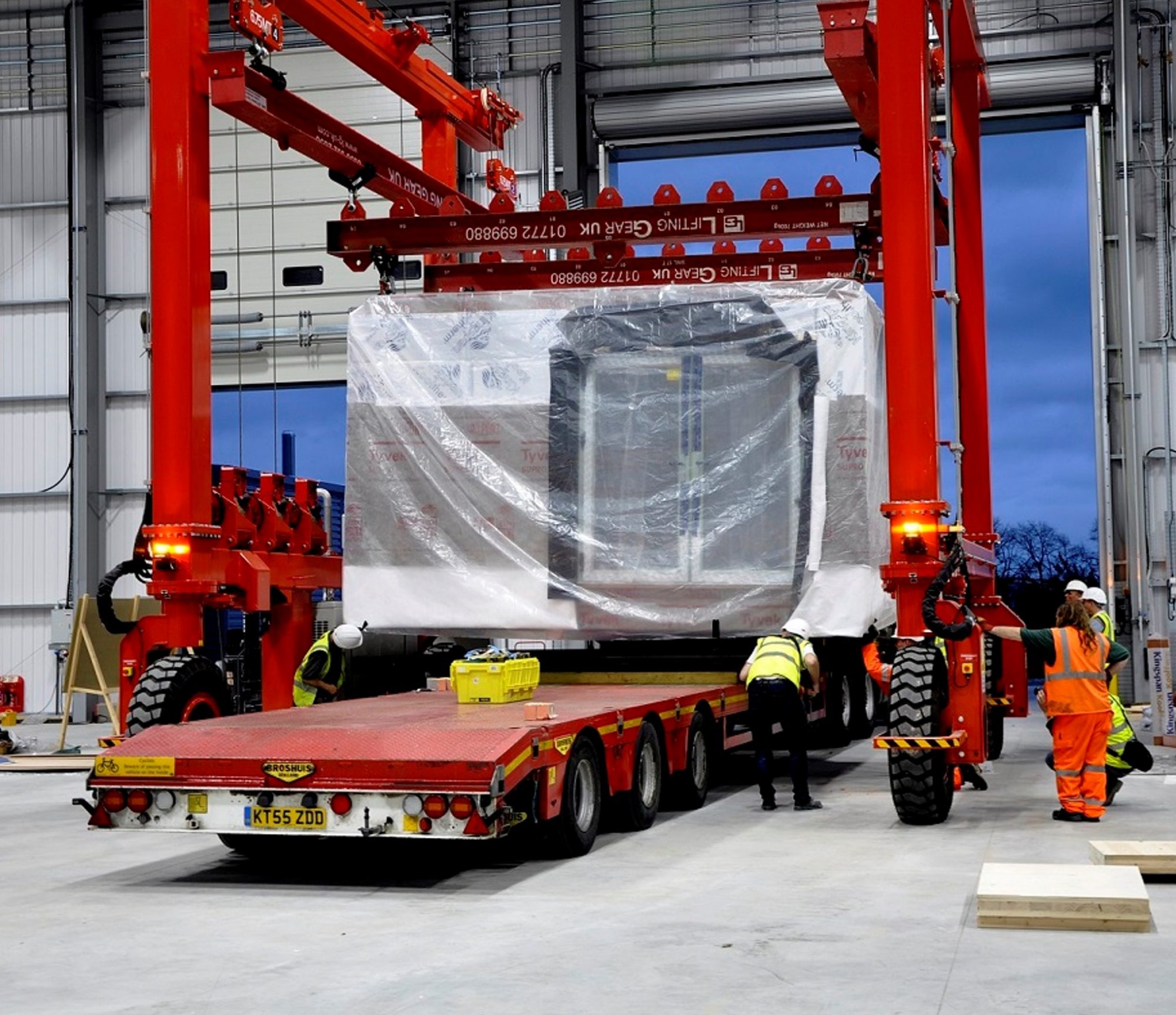
Procurement
The key challenge facing the developer who wishes to procure a modular development revolves around the point that the modular supplier’s product constitutes such a major element of the build in a single package, completed off site.
Typically, the developer would be expected to make significant payments in advance before the modules reach site, creating contractual and insurance risks. The need to design to suit a modular system institutes a two-stage procurement process, which the developer may consider limits best value versus the typical competitive tender process. In the case of Beechwood these procurement issues were neatly sidestepped by Swan, who had the foresight to set up their own factory, offering them the benefit of control over design, quality and costs and the potential for a regulated development pipeline.
As illustrated in the Beechwood example, many modular developments still use traditional cladding which can easily make new homes indistinguishable from traditionally built ones. However, this can severely impact on construction speed and costs, undoing many of the benefits of factory production. While it may be possible to manufacture pre-clad modular units, there are other issues to factor in – such as the risk of damage in transit or when lifting due to racking – resulting in a preference to apply external materials on site.
The use of brick slips and brick panelised systems, although tried and tested, currently adds expense, so it is rarely adopted in instances where wet trades can easily be deployed. Going forward, alternative approaches must be developed to address this through new material technology and supply chains.
For those in the housing sector that measure their time in decades rather than years, the expression housing crisis has been a constant. This alone should be enough to impel housing developers, constructors, and manufacturers to strive for improved ways of working to deliver more and better homes. Combine this with a myriad of other issues facing the British construction sector, including the climate emergency which requires us to work towards providing zero carbon homes; the Hackitt report; sweeping reforms which demand the complete overhaul of the way we design, construct and validate; and Brexit exacerbating skilled labour shortages; it is clear that significant change is required to the procurement of housing. Off-site manufacture and modular construction are not the only answers but are certainly crucial tools in the box and are fit for purpose to meet the future demands of the housing industry.
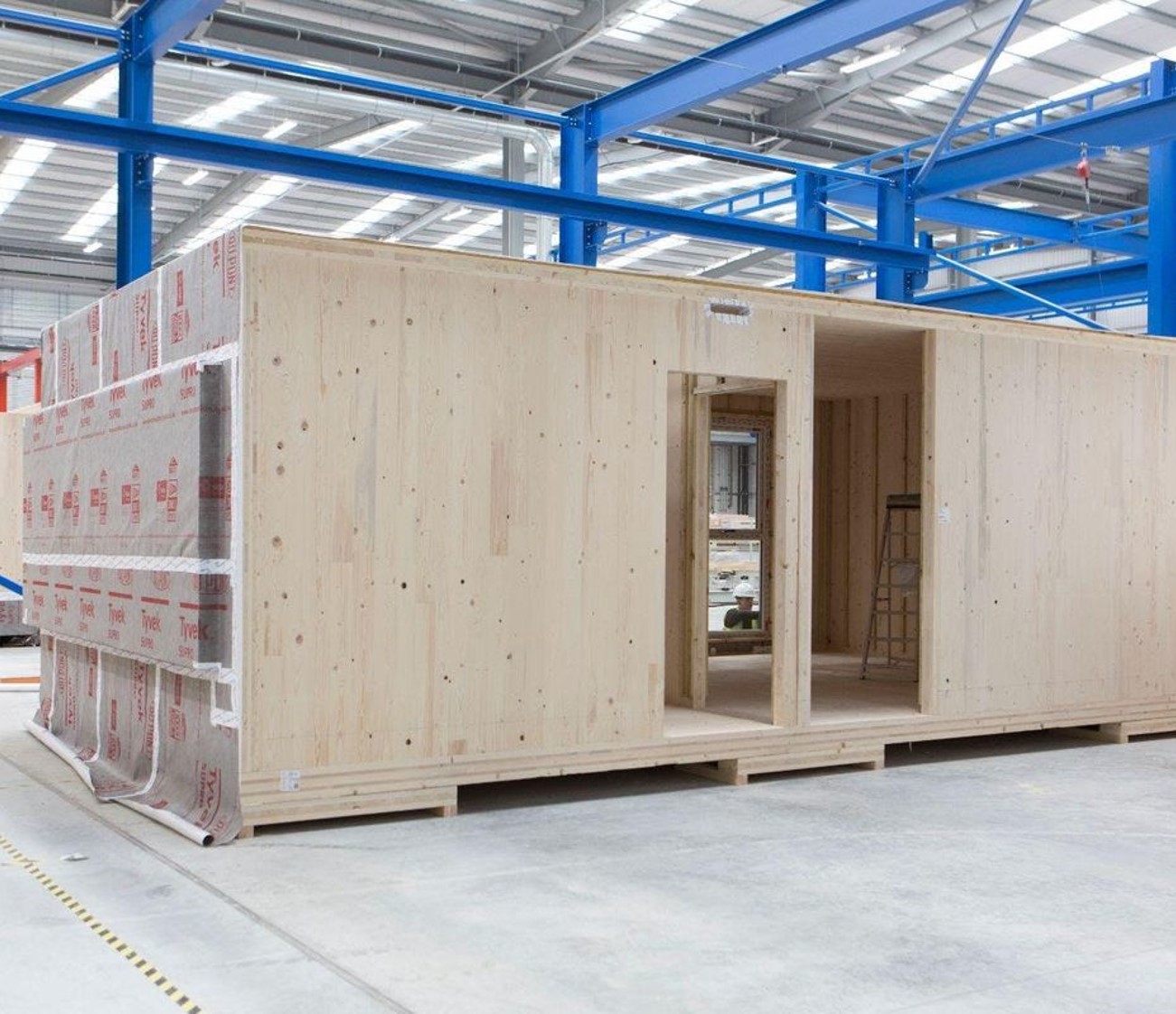
COVID-19
The construction industry and associated disciplines have adapted quickly in many ways to the consequences of the COVID-19 pandemic. However, lockdown led to the immediate closure of most construction sites, and despite sites now being operational again, the everyday experience is very different and we have seen a significant impact on efficiency.
Restraints caused by social distancing and a scramble for new best practice guidance to manage workflow and teams on site safely will have a significant impact on programmes and costs for many months to come, and site processes may never be quite the same again. What the pandemic has shown us is that society as a whole and the construction industry in particular needs to have more resilience built into their systems to be able to cope with the unexpected as well as predictable challenges. A construction industry with increased use of off-site manufacturing, with its factory-based controls and processes, will be better positioned to cope and adapt in a way that enhances rather than reduces productivity.
BPTW advocate the application of off-site manufacturing wherever possible in all its various forms, including modular construction. However, it imperative that we use our knowledge and experience to advise our clients when modular construction might not be suited, such as where adequate standardisation or volume may be hard to achieve. Developers and design teams must embrace off-site construction methods to strike the optimum balance between economies of scale delivering efficiency, design quality and the potential for architectural delight. Designers must take advantage of work stages that might be reduced, and exploit the space and time liberated to apply their creativity to other areas, ensuring we continue to create exceptional homes and places.
Developers in the Victorian and Edwardian eras, as well as during the 1930s house building boom, relied heavily on the repetition of standardised pattern-book homes which responded to the needs and aspiration of their day, assembled into urban and suburban tree-lined streets. These homes remain much sought after today, often in preference to new build houses on offer, which illustrates that standardisation is not the enemy of good and lasting design.
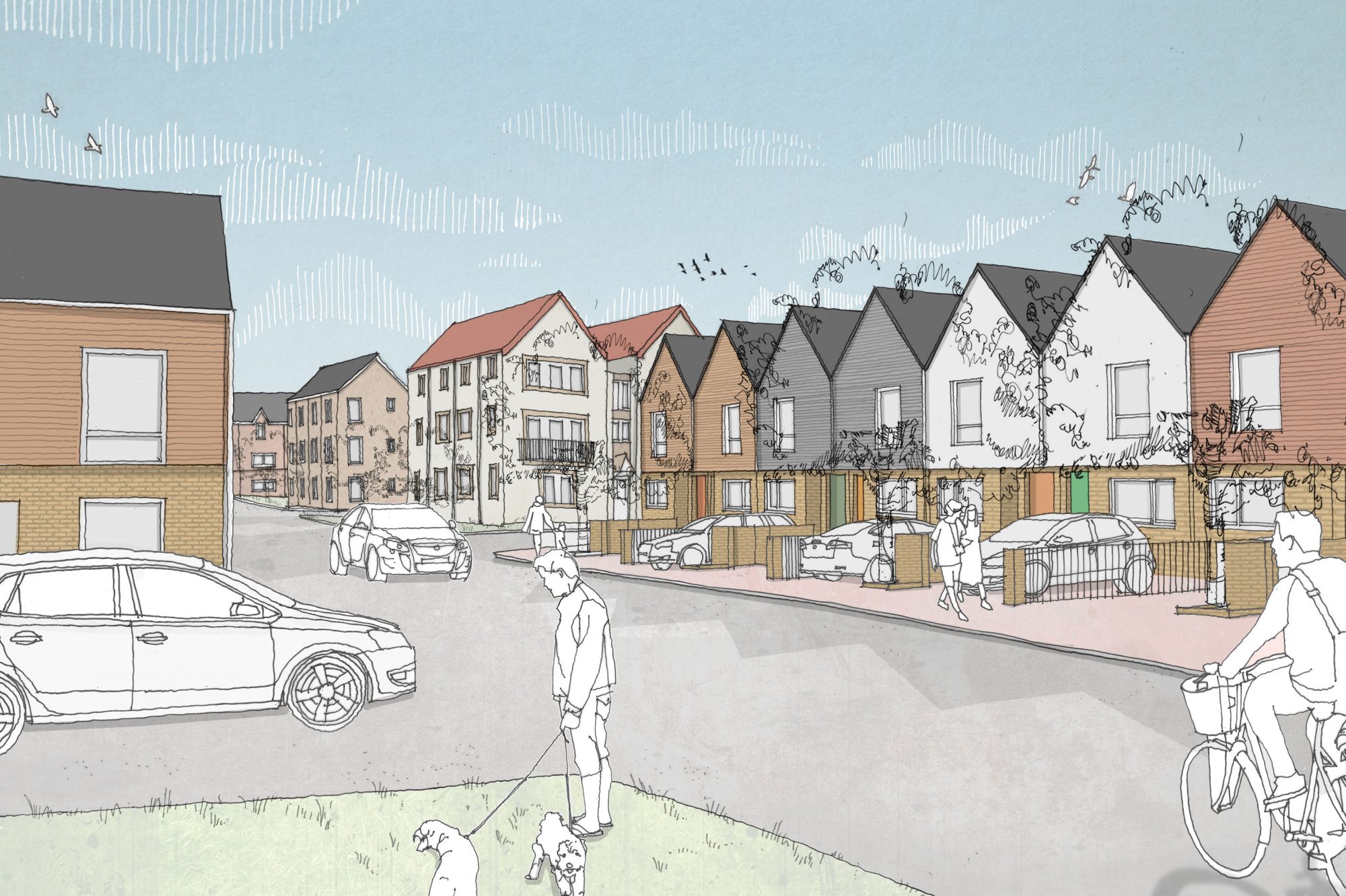